结构疲劳分析疲劳耐久分析疲劳寿命分析
业务范围:
机械重工结构疲劳分析、车辆行业疲劳耐久分析、工业设备疲劳分析等各领域疲劳寿命分析仿真服务。
疲劳分析应用案例:
1.车辆疲劳耐久性能开发
疲劳寿命分析是有限元仿真的一个重要类型。汽车疲劳耐久分析是为了考核整车、系统、子系统和零部件可靠性的一组试验,疲劳寿命分析是耐久性试验考核的重点,也是决定汽车品质的关键因素,汽车90%以上的零部件损坏都属于疲劳损坏。
上图是传统台架试验,传统的汽车疲劳性能开发方式,即在样车制造完成后进行可靠性试验验证,对发现的问题进行设计整改,是再试验、再整改的反复过程,存在时间滞后、开发周期长以及资金投入大等问题。
基于有限元的疲劳仿真分析思路
用有限元分析进行疲劳分析,其基本思路是:首先进行静或动强度分析,然后进入到后处理器取出相关的应力应变结果,在后处理器中再定义载荷事件,循环材料特性,接着根据所需要的疲劳准则对每一个载荷事件进行寿命计算,最后根据累计损伤理论判断是否开始破坏。
2.火车吊挂设备-电源分配箱的寿命预测
底盘零部件疲劳寿命分析云图,
这些零部件以及整车的动态时域载荷对零部件及整车进行疲劳寿命仿真分析,判断其是否满足制定的疲劳耐久性目标要求,若不满足则需要进行优化设计,直到分析结果满足要求。
车身疲劳分析损伤云图
从白车身损伤云图看,白车身最大损伤值为0.103(等效寿命2.9万公里),超出目标值,最大损伤部位在顶部第七横梁下板孔位置,其它部位损伤均小于目标值。
车身焊缝疲劳分析损伤云图
白车身焊接缝最大损伤值为1.678,超出目标值,黄色区域损伤值大于0.5,小于1,红色区域损伤值大于1。
底盘疲劳寿命分析
底盘焊缝疲劳分析
车架焊缝疲劳分析
如图再发动机托架焊接处损伤较大,其余部位均小于0.1。
应用有限元分析技术,疲劳分析工程师经过20轮次长达200小时的方案优化计算,最终使得疲劳性能在满足设定目标要求前提下,耐久性又提升了50%左右。经过台架试验及实车道路试验验证,未出现疲劳开裂问题,耐久性有了大幅的提升,验证了仿真分析的精度。
2.基于Fluent+ABAQUS+FE-SAFE实现压力脉动疲劳分析
3.基于FE-SAFE+ABAQUS实现齿轮疲劳耐久分析
齿轮啮合过程中,齿面易产生表面疲劳磨损。基于疲劳磨损的最大切应力理论,最大剪切应力产生于接触表面附近,如果最大剪切应力超过材料的屈服应力将发生塑性应变,并伴随着外载荷的反复作用,将在发生塑性应变处出现裂纹;因此剪切应力低于屈服应力将不易发生表面疲劳磨损。
疲劳分析类型
应力疲劳仿真(单轴/多轴疲劳,主应力疲劳,VonMises应力疲劳,BS7608焊缝疲劳,DangVan无限寿命疲劳)
应变疲劳仿真(单轴/多轴疲劳,最大主应变疲劳,最大剪切应变疲劳,Brown-Miller组合应变疲劳,铸铁疲劳)
询价需提供:
1.三维模型图档(UG,Solidworks、Pro/E、CATIA、step皆可),可以签保密协议,如果图不方便发,相关测试零件图片也可以。我司会履行严格保密义务。
2.测试条件说明ppt文档,将需要测试的内容叙述清楚,主要包含:固定约束条件、装配链接方式、边界条件、载荷加载方式、仿真关注区域、零件材料清单、仿真报告格式要求等。
3.软件要求、有限元仿真技术要求、交期要求等。
申明:本文原创自乐图智造官网,转载请注明出处。
查看更多案例: 散热分析 热仿真分析 压铸模流分析 模态分析 CFD分析 电磁场仿真分析 跌落分析
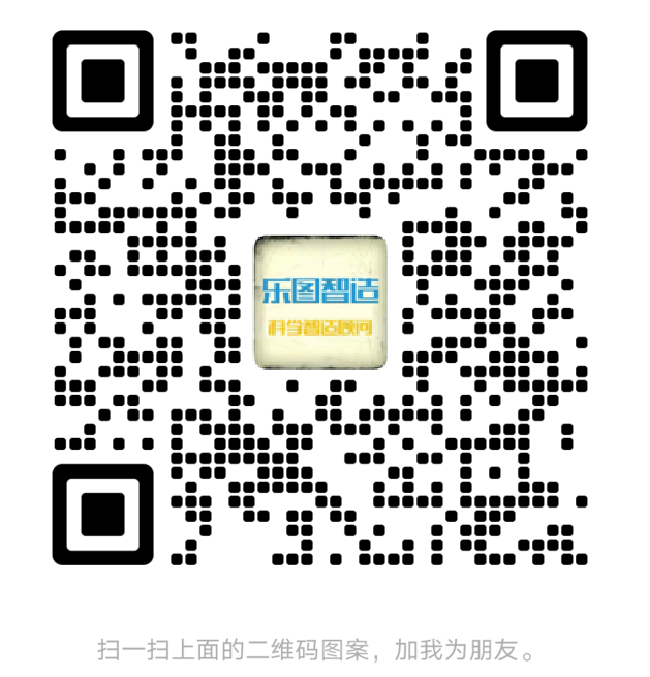
乐图智造科技(苏州)有限公司
199 4191 2022
业务咨询/技术咨询/交流建议
扫码微信咨询,24小时期待你的声音