【压铸方案开发】铝合金横梁浇排设计方案开发
应用magma铸造模拟软件开发铝合金横梁浇排设计方案
行业背景趋势:
汽车轻量化的要求,导致了零部件向着功能集成化,重量轻量化,结构复杂化的方向发展。目前零部件的开发周期要求越来越短。传统的根据经验进行的新产品制造开发更像是一种试错法,通过多次试制验证来进行方案的优化,进而改善产品质量。这种方式消耗了大量的人力,物力,精力和时间,造成了严重的浪费,已经不满足新项目的开发需求。
产品背景与要求:
铸件基本尺寸为416mm×182mm×22mm,质量为4.45kg,材料牌号为ADC12。此产品整体壁厚较为均匀,平均壁厚为4.3mm。产品需要装配和焊接,所以对孔隙率和轮廓度要求非常高。根据产品的特性和质量要求,需要设计一个最佳的浇注系统,保证金属液顺序充型,最大限度的降低流动孔隙率和气体孔隙率。同时该产品中间存在非常大的窗口区域,对金属液充型造成了极大的阻碍,所以也要非常关注产品末端的成型状态。
通过使用MAGMASOFT将开发过程可视化,透明化,通过对不同的工艺参数和不同的工艺方案对比分析,进而得到最佳的工艺方案组合。这种方式可以提前预测产品将会出现的问题,并在方案前期进行改善措施,以此减少试模次数。以软件推荐的最优方案为指引进行试制,结果表明,原本需要多次试制和改善的方案,实现了T0试模后直接量产的状态,最大限度的节约了成本,压缩了开发周期。
图1:四种浇注设计(A到D)和对应的75%填充的填充结果
浇口方案评估筛选:
其中对4个方案进行分析和判断如下:
方案A 共五个浇口,浇口分布均匀,进浇平衡,可实现整体进浇。压力也相对传递均匀,保证致密度。需注意最末端填充区域,有冷料堆积充填与排气不良风险。
方案B 共三个浇口,产品大体积区域对应大浇口,保证充填质量与压力传递。但厚大浇口容易造成局部温度过高,引起变形及对模具形成不良影响。同时此摆放位会拉长充填行程。
方案C 共三个浇口,产品大体积区域对应大浇口,保证充填质量与压力传递。但厚大浇口容易造成局部温度过高,引起变形及对模具形成不良影响 。
方案D 共三个浇口,产品大体积区域对应大浇口,保证充填质量与压力传递。但厚大浇口容易造成局部温度过高,引起变形及对模具形成不良影响。
根据设置的工艺条件,软件完成四种方案的计算后进行多维度的大数据统计,根据铝液流动顺畅的评价,推荐最佳进浇方案为方案A。
图2 进浇方案评估结果
排溢系统方案筛选:
在确定初始排溢系统后,再次进行流动模拟,发现现有的排溢系统不够完善,产品末端存在高气压。高气压区域有非常大的气孔风险,将会严重的影响产品成型,焊接和装配。于是根据模拟结果优化排溢方案,在高气压区增加排气道来降低气体聚集的风险。实际生产中需要辅以真空工艺,按照此工艺设计基础,再次模拟,观察和对比优化前后的产品气压分布,发现增加排气道及增加真空工艺后,原高气压区域的气压值由5000mbar降为1000mbar,结果显示高气压问题得到有效的改善,详见图3。
图3 排溢系统优化和优化模拟结果对比
在确定好浇排系统之后,还需要对压铸工艺参数进行设计和计算。MAGMASOFT的自主优化工具,使得工程师能通过了解工艺变量对铸件质量的影响,更为省时省力地探索更大的设计空间,进而找到最优的压铸模具和工艺布置方案。与传统模拟不同,自主模拟只需要工程师设定一次模拟,但是,很多模拟运行将覆盖全部工艺窗口。该软件自主地挑出可能的设计,进行分析并采用统计数据方式汇总所有结果。
DOE优化压铸的工艺参数:
基于浇排系统设计完成的基础之上,借助DOE自主优化工具进行压铸工艺参数的优化。高速速度是影响铝液填充和产品质量的关键参数。以高速速度的DOE优化过程为研究对象,进行分析。设定高速速度在3.5-4.0m/s之间,迭代步长设定为0.1,以降低浇口速度及减小冷隔缺陷为目标对象。通过软件进行大数据分析与统计后,推荐出最佳成型工艺参数,选择高速速度3.5m/s既可以满足浇口速度低,降低模具充蚀,又可以保证产品的质量。
通过MAGMASOFT的浇注方案及参数设计的标准流程,完成了产品的浇排系统设计及压铸工艺参数的优化,以此数据为指导,用于实际的验证。首次试制选用1600T压铸机,并辅助以真空系统,按照DOE优化设计的压铸参数进行试制。图9为首试的铸件图。通过对内部品质的x光探测发现铸件内部的品质比较理想,内部品质缺陷如气孔、缩松以及缩孔均符合ASTM F_505 1级的标准。产品经过焊接验证,焊接区域未发生有焊接缺陷,证明产品的内部含气量很低。产品首次试制成功。
本文以压铸铝合金横梁的开发过程为例,通过使用MAGMASOFT将开发过程可视化,透明化。通过这种方式可以提前预测产品将会出现的问题,并在方案前期进行改善措施,以此减少试模次数。通过对横梁的浇排系统及压铸工艺参数的DOE优化,以软件推荐的最优方案为指引进行试制,产品首次试制就达到了量产的状态,最大限度的节约了成本,压缩了开发周期。
联系咨询,探索科学铸造方案,一起创造更高附加值
乐图智造科技,产品性能优化,有限元分析工程服务,软件销售,提供科学的数值信息化技术解决方案,
申明:本文原创自乐图智造官网,转载请注明出处。
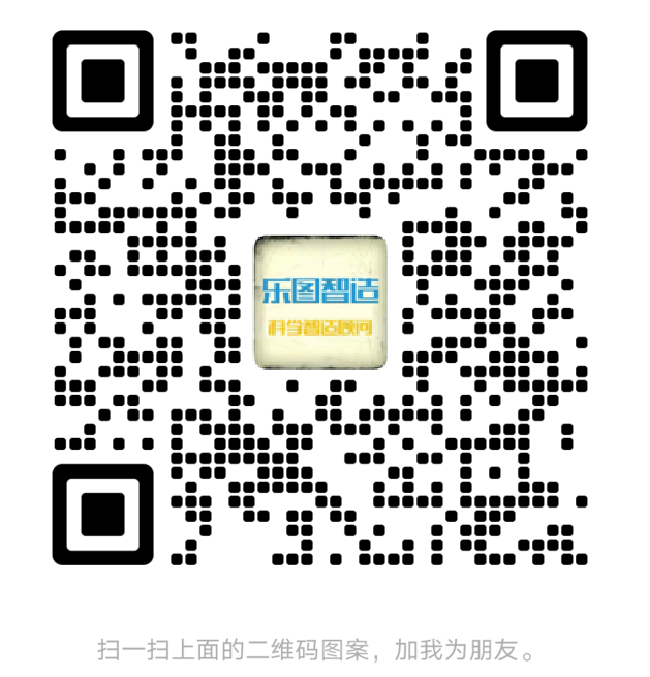
乐图智造科技(苏州)有限公司
199 4191 2022
业务咨询/技术咨询/交流建议
扫码微信咨询,24小时期待你的声音